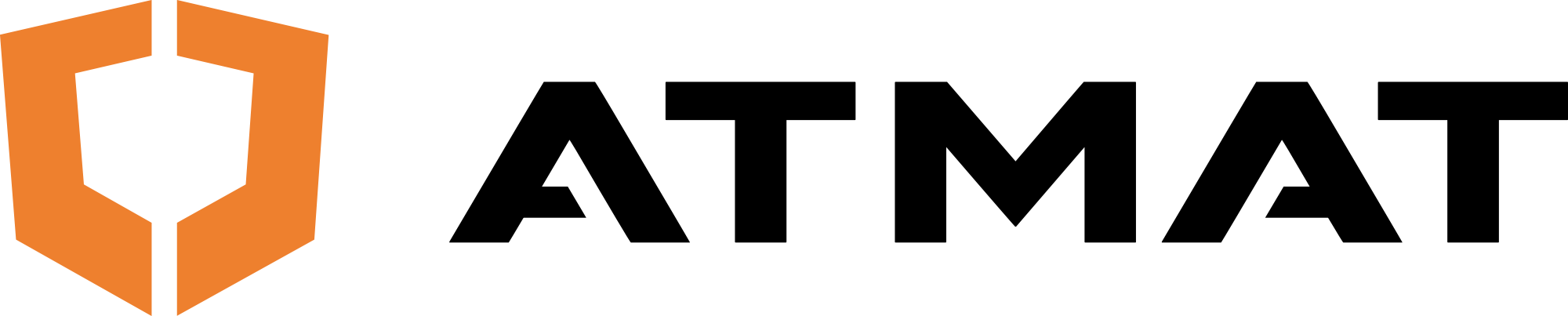
Extruder and head assembly tool with ABS 3D printed parts.
- Analysis
- Research
- Implementation
A few words about the project
The tool for assembling the entire extruder component and the 3D printer head is designed to ensure accuracy and speed during the assembly work. For the realization of individual elements, we used FDM additive manufacturing technology.
The concept of the project was created after the final part of designing a new 3D printer and building the prototype of the device. After successful tests, we started the serial production of the devices, and at the same time, we implemented optimization processes. They were concentrated on improving production. One of the innovations was the implementation of this tool.
The task was to develop an instrument that will speed up and facilitate the process of serial assembly of the module for ATMAT 3D printers. The tool was to be designed in such a way that it could be easily adapted to other types of extruders found in other printers.
Who was our client?
ATMAT is a dynamically developing Polish manufacturing company, specializing in industrial engineering. ATMAT's Serial Products Department designs and manufactures standard and large-scale 3D printers in FDM technology. To build them, it uses dedicated solutions that are designed to optimize production time and costs.
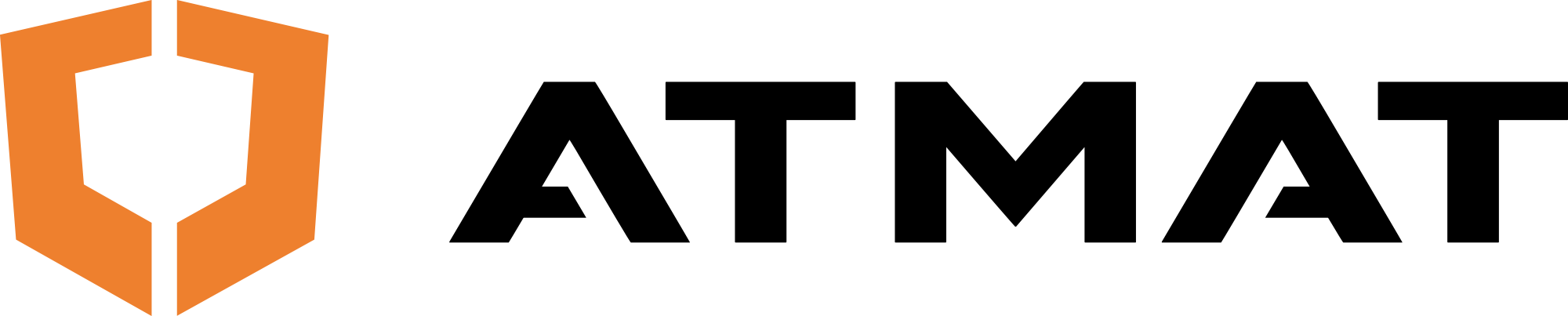
Our challenge
The project aimed to create an extruder
and head assembly tool that would help
optimize printer production and shorten
assembly time.
As part of the project we did the following work:
- design of the tool,
-
ordering premade components,
-
printing parts from ABS material,
-
assembly,
-
tool tests together with the measurement of an extruder and head assembly time,
-
-implementing a tool to improve the assembly of printer components.
Our solution
The implementation of the tool helped to improve the extruder and the 3D printer head assembly process. This reduced the assembly time of this component by 25%.
Fast and accurate fixing of the extruder plate is possible thanks to the use of fixing pins and knurled knobs. This also enables subsequent disassembly. The fixing of the extruder also gives the fitter more flexibility and no restrictions. Thanks to the implementation, the comfort and convenience of work have increased. In addition, the entire beam, to which the extruder is attached, has been supported and ball-beared on both ends. This gives the possibility of rotation of a 360-degree angle, which allows the fitter to easily access the screwing of the component. Locking pins are also used, what allows the position to be stopped every 20-degree angle.
For the construction of the stand, 6 models printed in 3D technology from ABS material were used. The tool was designed in such a way that it can be easily adapted to other types of extruders found in other printers. For this purpose, you only need to replace 1 out of 6 printed elements to which the extruder board is screwed.
What was achieved??
01
Reduction of assembly time of the component by 25%.
02
Increasing assembly accuracy and protecting parts from scratches.
03
Provide lightness and mobility through the use of components printed in 3D with ABS.
04
Adaptation of the tool to install all types of heads.
What does the Client say about us?
Thanks to the use of ABS material, which is durable and haslow density, the tool is lightweight and mobile, which is a great advantage if you want to upgrade the assembly station to another type of tool. There are also comfortable carrying handles on the tool.
Łukasz Porębski
Junior Production Coordinator ATMAT