Jupiter
Unlimited space of opportunities
ATMAT Jupiter is one of the largest industrial-class 3D printer in Europe. Working area allows you to create objects up to 2 meters long. The device is equipped with the latest technological solutions in an industry-standard and designed to improve the production process and increase productivity. The machine is used in the industrial, architectural, automotive and aviation sectors.
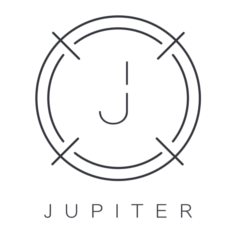
The largest working area
available in Europe
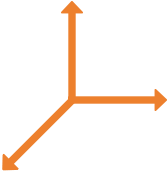
Printer working area
X:2000 Y:1000 Z:1000 mm
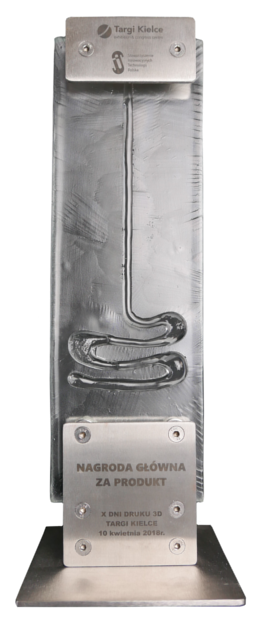
Grand Prize for the product
awarded during X 3D Printing Days
Granite bed with a high efficient heating system
An important aspect while designing a working platform was to obtain a stable structure that would guarantee proper adhesion between the working bed and created model. Working platform is equipped with a high efficient heating system, thanks to which the user can be sure that the whole work bed will be heated to the set temperature. Easy to disassemble construction of the bed allows to clean the surface easily, which affects on the correct process of creating prints.
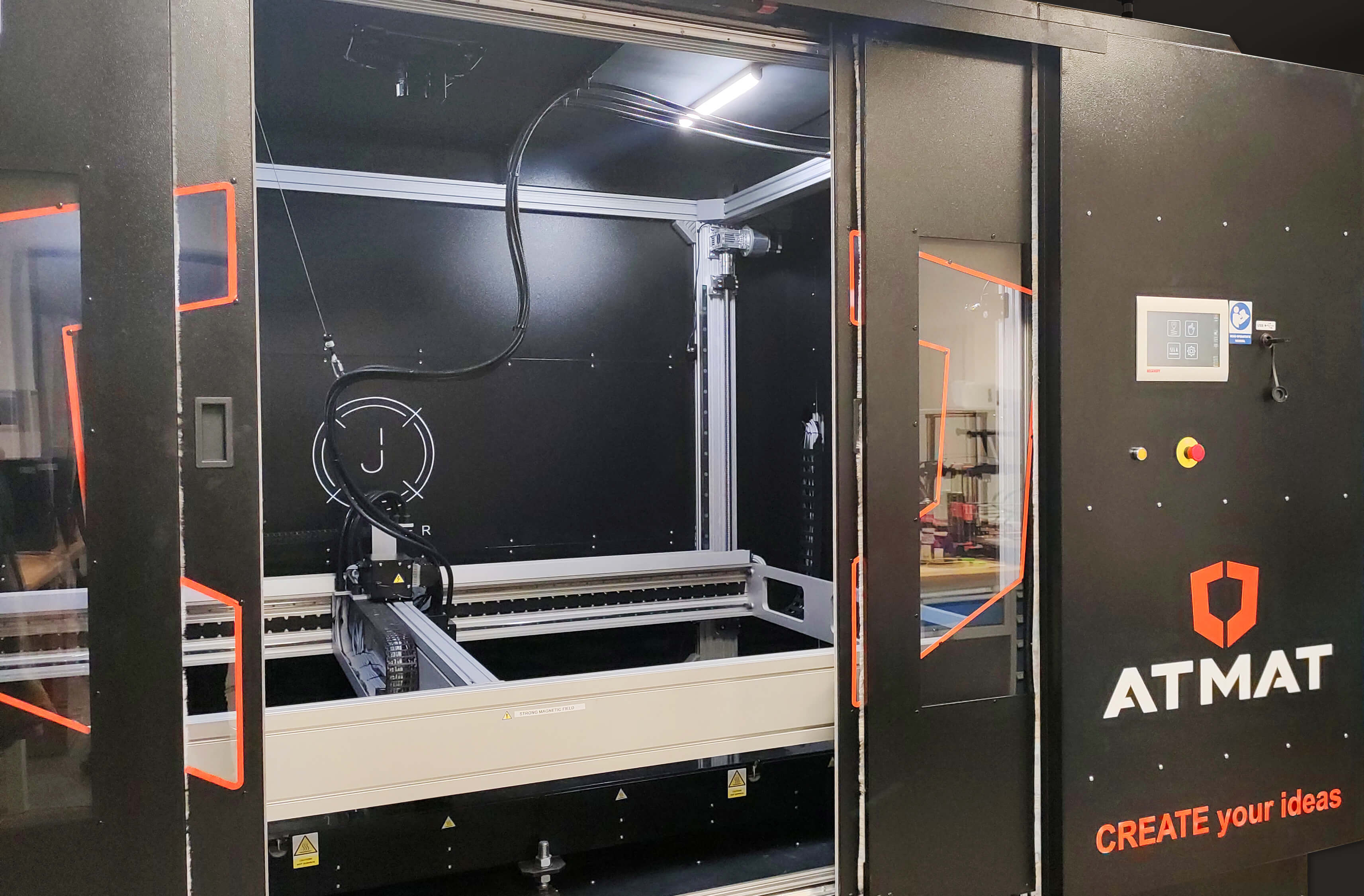
High-performance printing system
The printer is equipped with two heads specifically designed for large-scale production. The first head is a high-performance one, uses two extruders that have connected filament mixing tank Thanks to this, we can print at high speed, processing up to 0.5 kg of material per hour. The second head is an auxiliary one and has a single extruder, which is used to produce support structures or models requiring higher accuracy.
Filament case with dehumidifying containers
While designing a large-format 3D printer, it was important to assure the uninterrupted operation, which is the basic principle for long large-format prints. A filament case was created, which can hold 3 spools of filament, each up to 10 kg in weight. This solution guarantees long-term printing and continuous work without the need to replace materials. Additionally, the filaments are located in containers with dehumidifiers to limit the absorption of moisture from the air, which guarantees stability of their properties.
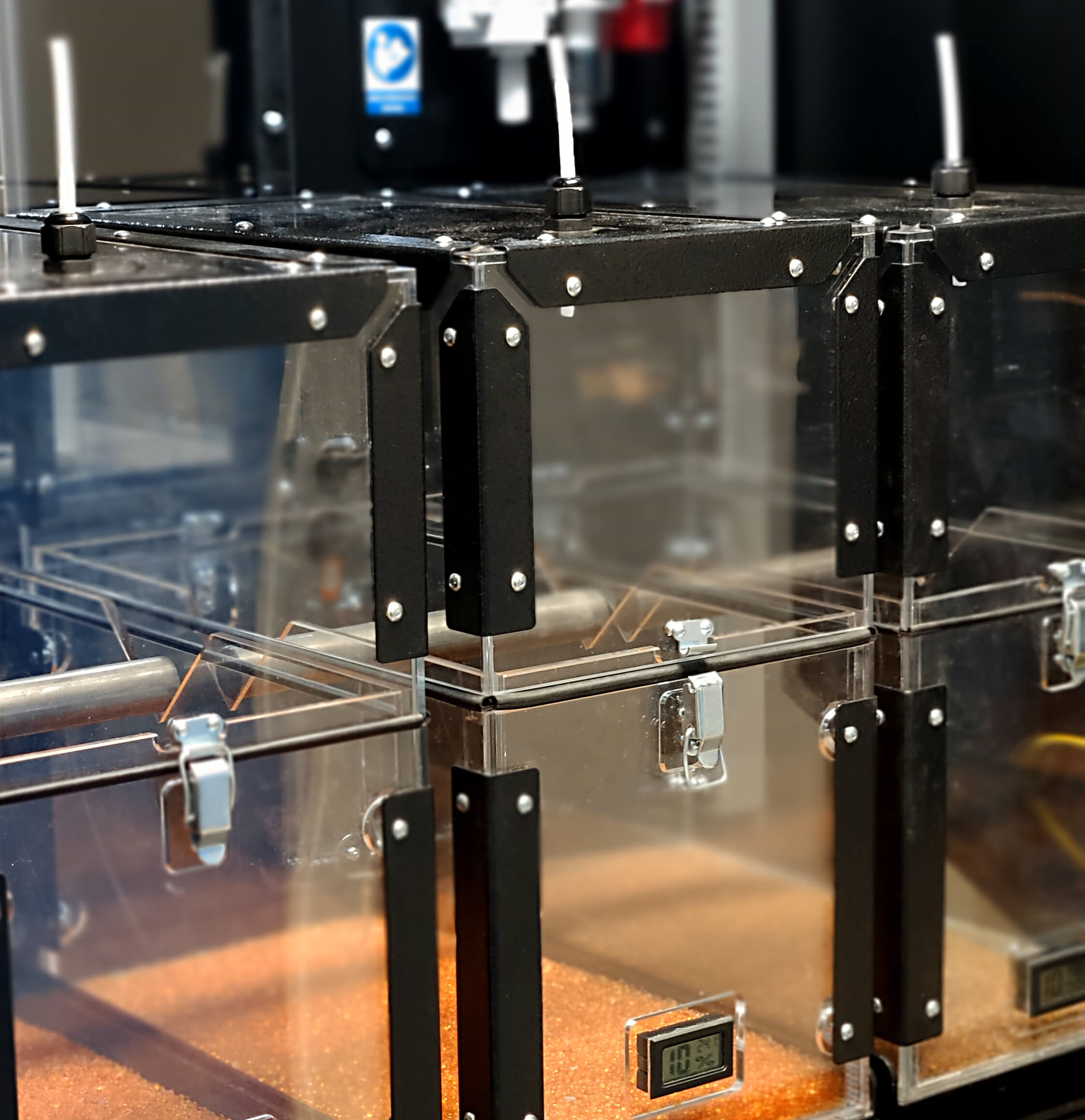
High-end servo drives
The linear magnetic drives on the X and Y axes have been replaced by Beckhoff high-end servo drives equipped with incremental encoders. Thanks to them the head works stably without losing its proper position, which makes it impossible for the layers to shift. The drive is transferred from the motor using a properly selected toothed belt, which does not stretch even at high printing speeds.
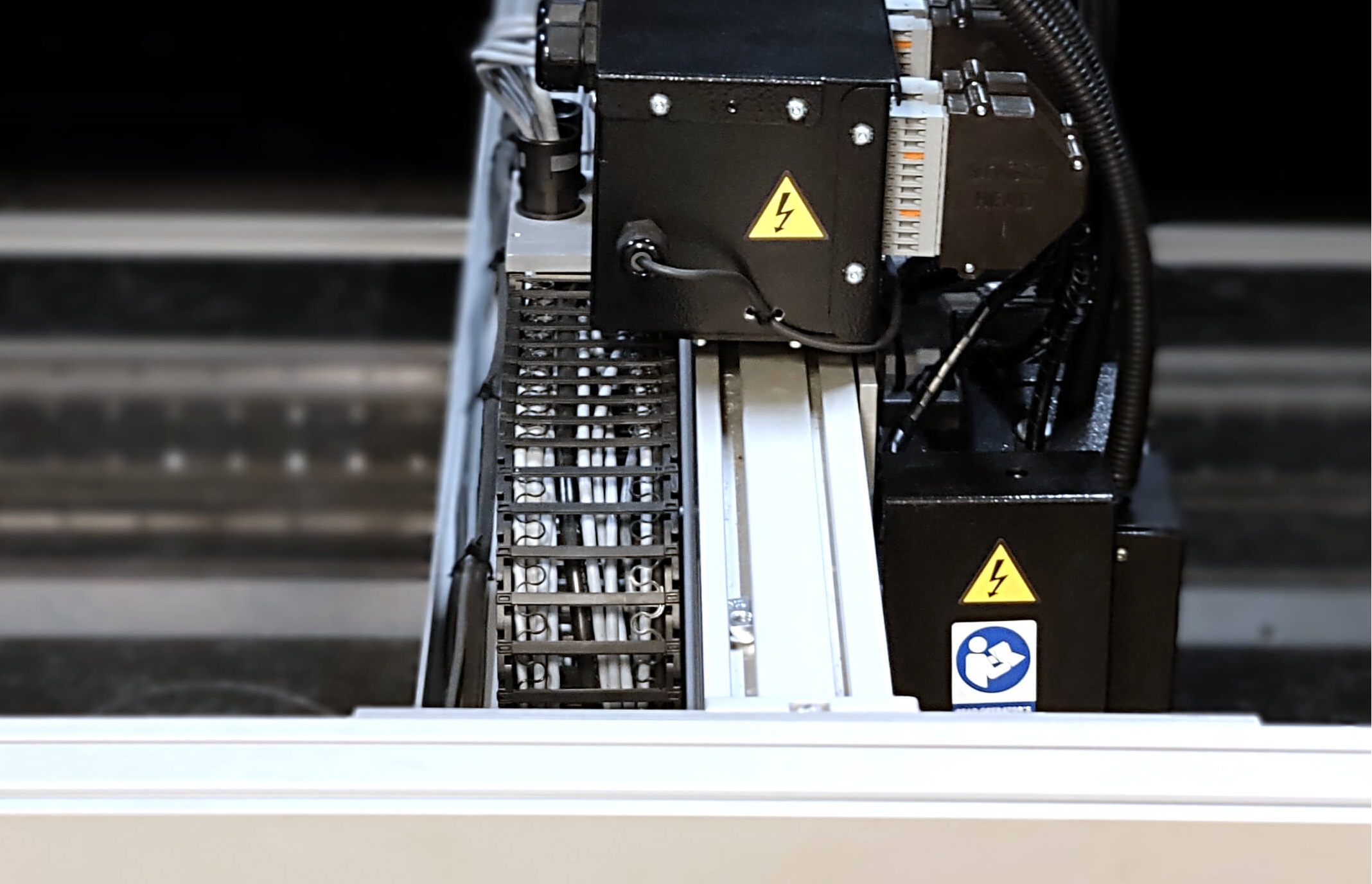
Intelligent machine control systems
The printer is equipped with intelligent control systems that allow the user to react quickly to problems that may arise. In case of power failure, the user can resume the printing process, which in case of prints lasting several days guarantees stability and uninterrupted production. The device is also equipped with a sensor of lack of filament flow, preventing sudden interruption of the printout, as well as a sensor for measuring the weight of the filament, allowing to predict the quantity of material needed to print the prepared model. Besides, the device is equipped with automatic nozzle height calibration, semi-automatic bedlevelling, semi-automatic filament exchange and automatic levelling of the XY frame.
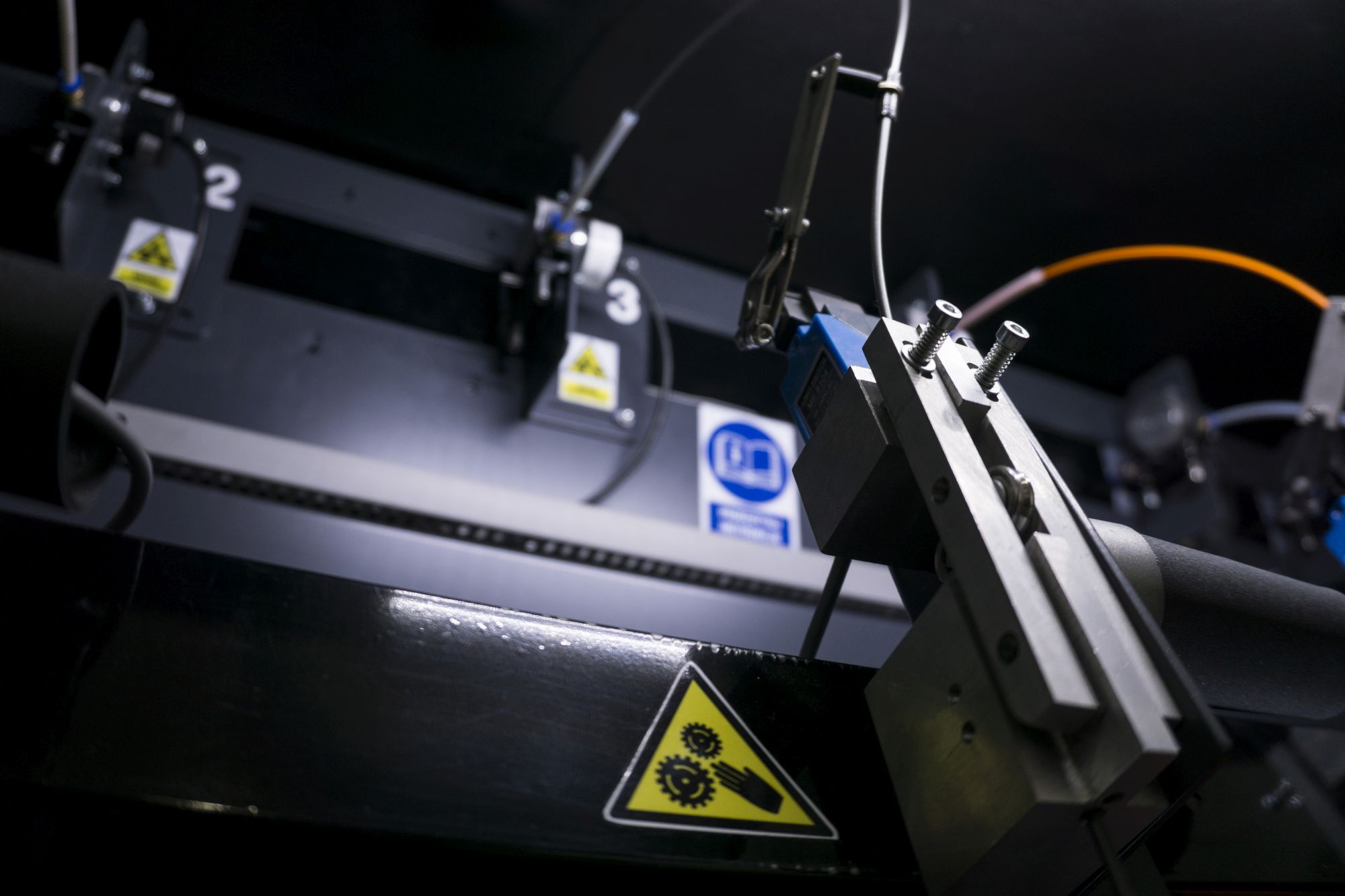
Thermally insulated, heated chamber
Maintaining a stable environment inside the printer's working chamber is a key function that impacts on the material used for printing. Thanks to the constant temperature in the printed model there is no processing shrinkage, causing delamination of the layers and adhesion of the model to the bed is improved.
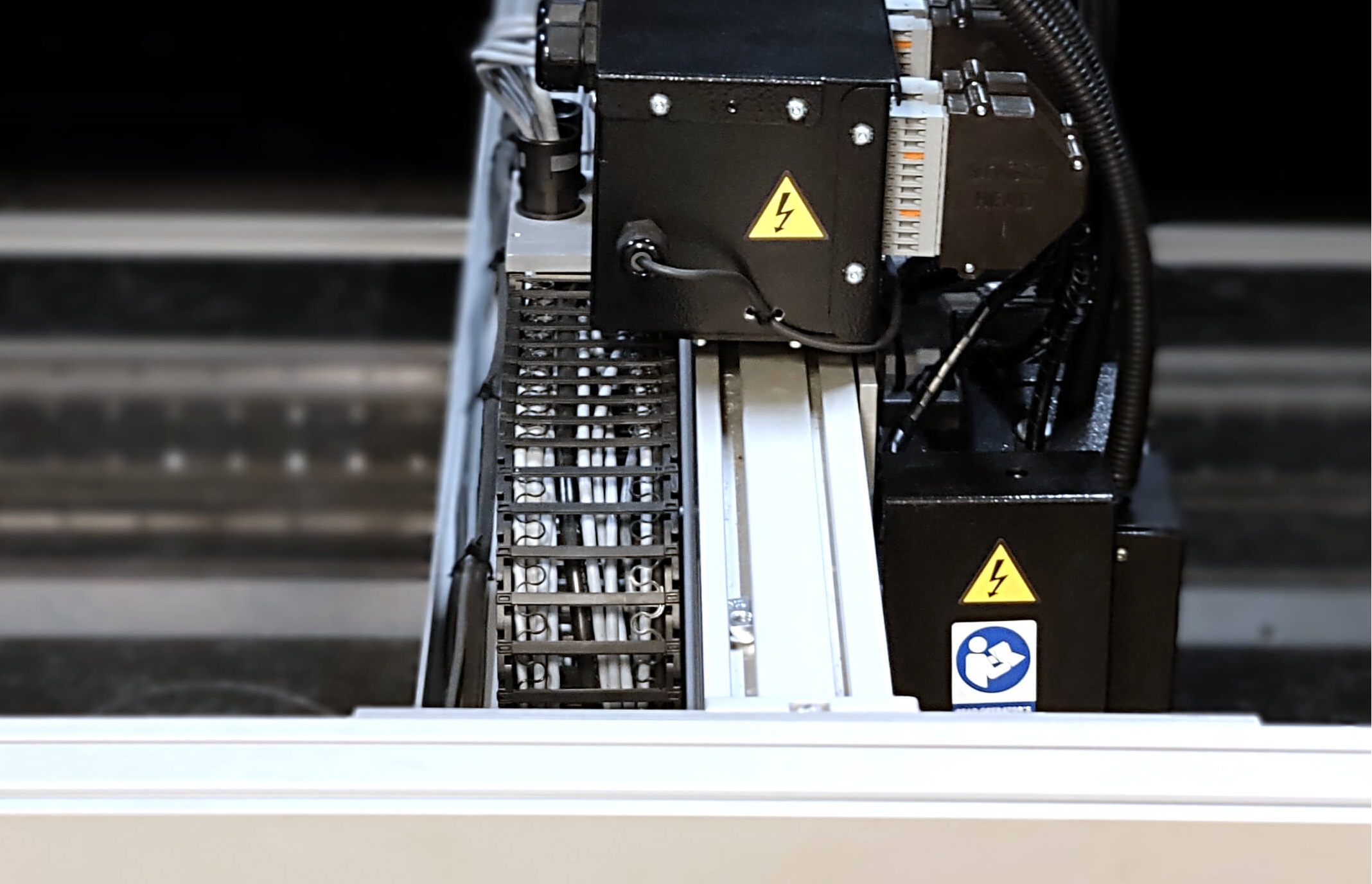
Restart of the printout after a power interruption
In case of a power outage, the user can restart the printing process. This functionality guarantees the stability and continuity of a few days' production processes and also reduces material losses. After the power supply is cut off, the controller saves the current position of the head, so when the current flow is restored, the user can resume printing in the control panel.
Discover unlimited space of opportunities
Technical specification | ||
Printing technology | FFF (FDM) | |
Specification of printers | Working area | X: 2000 Y: 1000 Z: 1000 mm |
Housing | Stable, aluminium sheet construction. Light column and safety switch on the outside of the housing. Separate cabinet for the materials. | |
Printing environment | Closed working chamber with temperature control | |
Max. chamber temperature | 45°C | |
Working bed | Automatic table calibration, 4-zone working platform heating system | |
Working bed material | Granite | |
Maximum bed temperature | 100°C | |
Head | Nozzle diameter |
Main printhead: 1mm, 1.5 mm, 2mm, Side printhead: 0.5mm, 1mm, 1.5mm |
Number of heads |
2 |
|
Number of extruders | 3 | |
Extruder type | Direct | |
Maximum head temperature | 340°C | |
Parameters of printing process | Layer height | 0.2 – 1 mm |
Nominal printing speed | 200 mm/s | |
HQ printing speed | 100 mm /s | |
Maximum passage speed | 500 mm/s | |
Positioning accuracy of the X/Y axes | 50 µm | |
Positioning accuracy of the Z axis | 10 µm | |
Software | Simplify3D | |
File extensions supported by software | .stl, .obj | |
Print materials | Materials |
PLA, PET-G, PA, ABS* *for printouts with limited geometry |
Material diameter | 2.85 mm | |
Filament form | Spool | |
Supported spool weights | 3 x 2.5kg/4.0kg/8.0kg | |
3D printer operation | Communication | USB 2.0 stick |
Supported formats | .gcode | |
Control | HMI with customized interface | |
Working environment temperature | 10 - 30°C | |
General data | Power | 400V/50Hz |
Max. power consumption | 27000 W | |
Average power consumption in operation for PLA | 2500 W | |
External dimensions |
3825x2375x2750 mm (width x depth x height) |
|
Weight | 3000kg |
Set of components
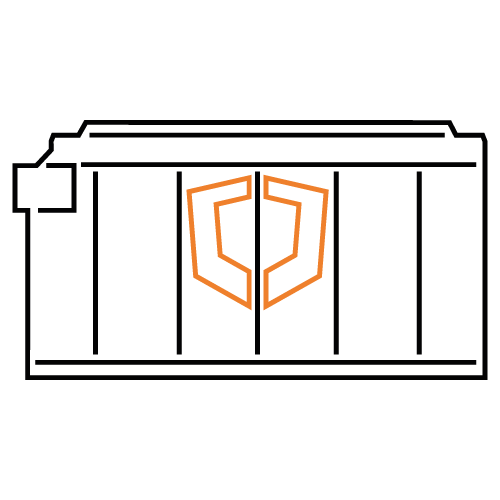
Jupiter 3D Printer
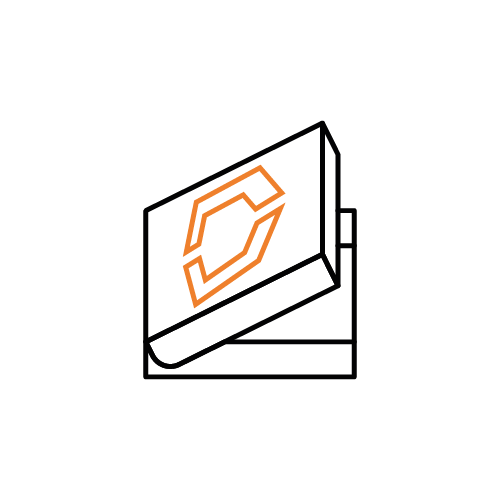
Exploitation kit
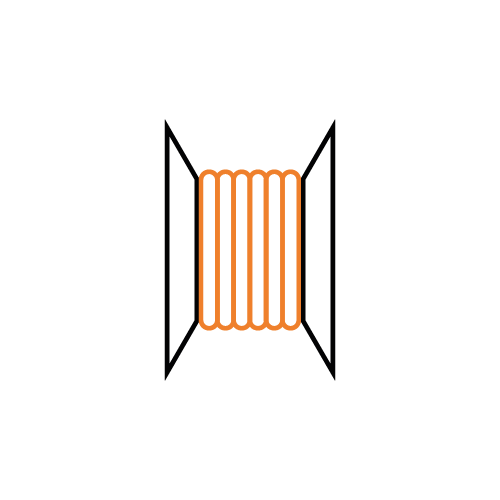
Filament (6 x 8 kg)
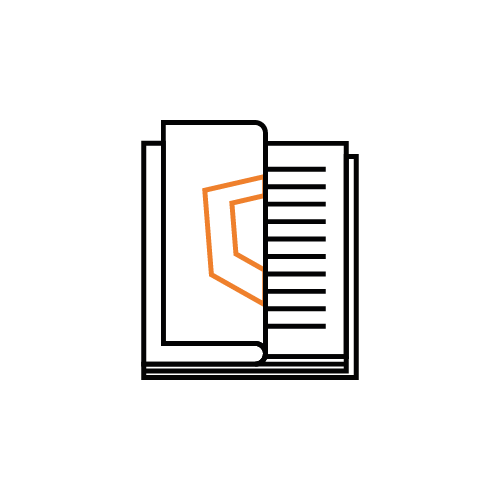
Technical documentation